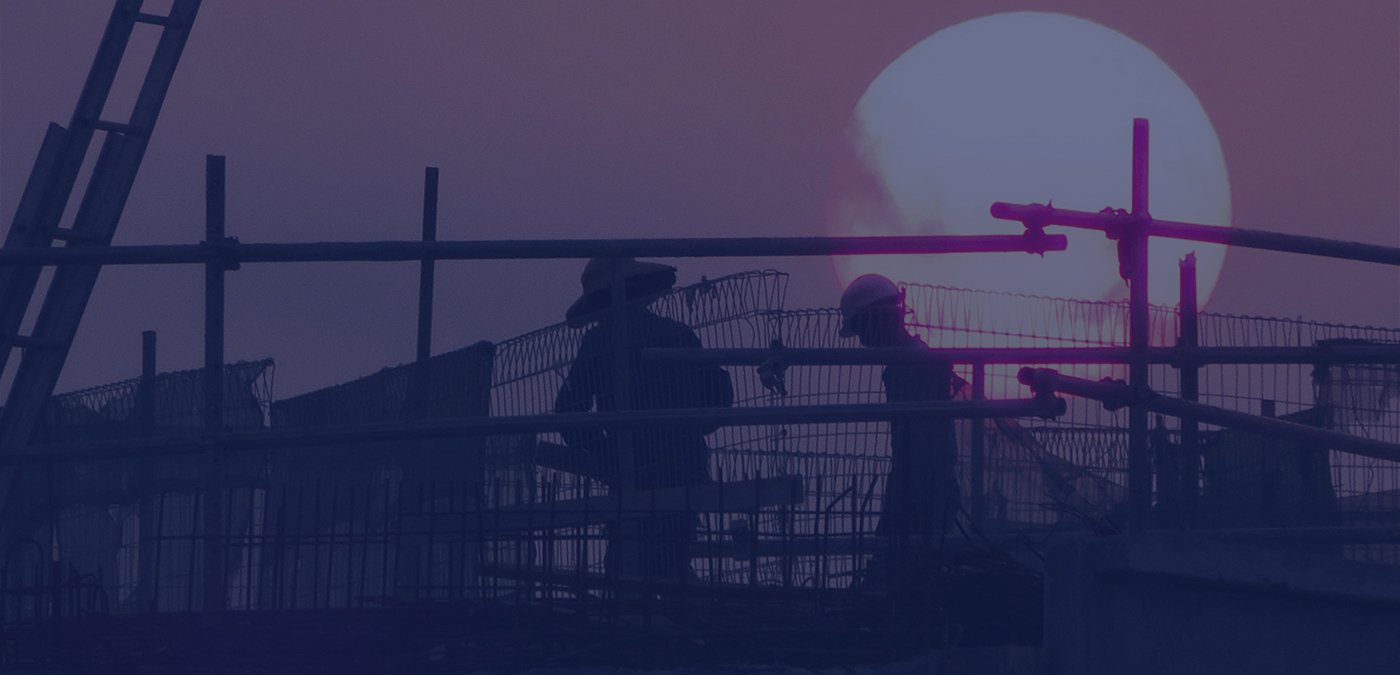
Seven areas that could boost construction productivity by up to 60%
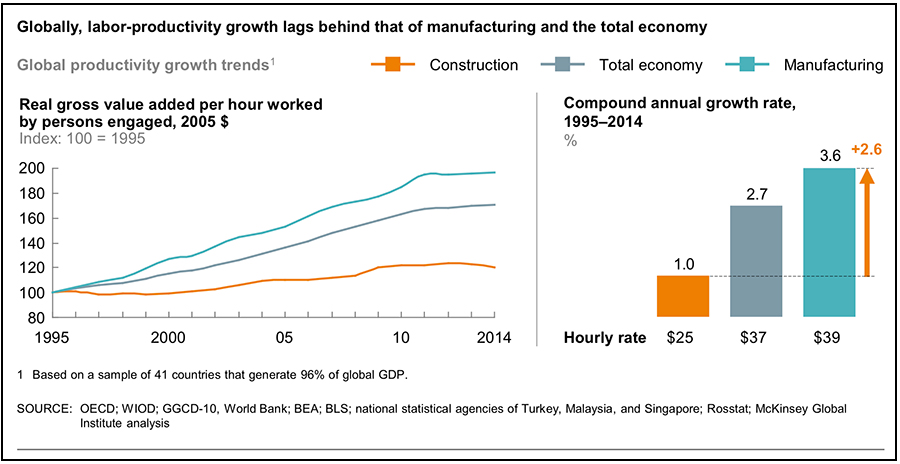
To the untrained eye, the data above makes for unpleasant reading but astute construction professionals are aware that the industry is on the cusp of some major global changes. According to Jan Mischke, a Senior Fellow at McKinsey & Company:
There is this change as we speak. I don’t think that anyone can predict whether it’s going to be changing over the next three years or over the next 30 years. But construction is changing. Digital is one of the biggest drivers of that change and one of the biggest necessities and opportunities for the industry, too.
And it’s not only digital transformation that is driving change. Government initiatives to drive growth are on the increase globally. The UK’s ‘Transforming Infrastructure Performance‘ initiative (TIP) is not only an example of how government is working with industry to drive growth but also how productivity growth is largely convergent on the seven areas highlighted in McKinsey’s Reinventing Construction report.
So what are the seven areas that can boost construction productivity?
Digital technology & innovation
Digital collaboration tools and software can be implemented very quickly for an immediate boost in worker productivity. In addition, output can be expanded through technologies such as Building Information Modelling (BIM), autonomous vehicles, drones for scanning, monitoring and mapping, advanced analytics enabled by Internet of Things (IOT) technology for improving on-site efficiency, as well as predictive analytics for cost and scheduling accuracy.
Reshape regulation
This would involve streamlining the permitting and approvals process, reducing informality and corruption, encouraging transparency on cost and performance and grants for innovation and training. Governments can also encourage best practice regulation leading to outcome-based, standardised building codes, and consolidating land to promote scale.
Rethink design
Restructuring the design process to include value engineering from the outset with greater focus on constructability, and repeatable design elements would make an immediate contribution to productivity. There is a move towards thinking about construction as a production system with increasing off-site manufacture and minimised on-site construction through extensive use of pre-cast technology.
Improve procurement and supply chain
A combination of adopting best practices from other industries and using digitally enhanced approaches can provide significant improvement. Better planning and greater transparency between contractors and suppliers would reduce delays and increase efficiency. Centralised procurement teams can drive economies of scale for certain products, while using digital technology to improve procurement and supply-chain workflows will enable more sophisticated logistics management and just-in-time delivery.
Improve on-site execution
Four approaches that are well known in the industry but have not been universally adopted are:
- Introduction of a rigorous planning process
- Agreed KPIs & performance metrics between owner and contractor
- Ensure all pre-work (approvals, project milestones etc) is completed before starting on-site
- Careful planning and coordination between disciplines on-site
Rewire contracts
The construction industry is plagued with a hostile contracting system and could boost quality and productivity by moving towards a more collaborative approach. To achieve this, tendering processes may be restructured to assess best value and past performances rather than cost alone. Establishing a single source of truth on projects for monitoring progress early helps minimise misalignments and enable joint corrective action.
Re-skill workers
The construction workforce is ageing and changing its makeup through migration. Construction companies should regularly train and reskill staff to use the latest equipment and digital tools. Apprenticeship programs go a long way to upskilling the workforce, especially at junior level.
So what’s the first step in boosting productivity?
It is clear that the construction sector globally is set for a major update. There are many factors driving the change from government initiatives to improving processes and technology, and as the sector evolves, many firms will fall by the wayside as the pressures of competing in a more efficient, tech-enhanced market intensify. Amongst the seven productivity boosting areas highlighted in McKinsey’s Reinventing Construction Report, construction firms should look at which changes are incumbent on government and which changes are incumbent on industry. Relaxing regulation, for example, requires work on the part of government whilst technology adoption requires work on the part of companies. Of the productivity boosting areas a construction company can address, technology generates by far the quickest and most significant improvement to productivity. Digital collaboration/ project management software in particular should be a key priority for construction firms as we enter a period of rapid change in the construction sector.